HARPS Newsletter – AuGUST 2021
Introduction from the HARPS Management Team
Find out about the audit process and what goes on behind the scenes from the perspective of the HARPS auditor and the Certification Body. Gain insight into the steps involved prior to the audit taking place, right through to receiving your HARPS certificate, and what happens after the auditor has left your premises.
In addition, you’ll find an update on our progress with the development of Version 2.0 of the HARPS Standard based upon the feedback received from the public consultation. Learn more about the review process and the role of the HARPS Technical Advisory Group (H-TAG) in developing the next version of the standard.
We’ve lined up a series of interviews with our H-TAG members, to learn more about why they joined the H-TAG, what they hope to bring to the group and their experience with the H-TAG to date.
Finally, learn more about the fee structure for HARPS and how the management of the program is supported financially.
Feel free to share your thoughts, opinion, or queries with HARPS by clicking here or contacting the HARPS Helpline on 1300 852 219.
Update on the Review of HARPS Version 2.0
The HARPS Technical Advisory Group (H-TAG) have been methodically working through the feedback received during the HARPS Version 2.0 public consultation process. Recommendations have been developed adopting a science-based approach and ensuring elements are pragmatic and efficient (in terms of implementation) for businesses audited to HARPS, whilst still meeting the needs of the HARPS Retailers and their customers.
As the H-TAG is large, with 18 members in total, sub-groups have been formed to allow members to delve further into specific areas that require more attention and detailed technical review. These sub-groups review elements that have generated the most feedback, including duplication of elements with the GFSI program, training, the withholding period for untreated manure application and the scope of HARPS for Tier 2 suppliers. The sub-groups then present their findings to the broader H-TAG before recommendations are finalised and presented to the HARPS Retailers. The role of One Direction ANZ in the review process is to facilitate meetings and provide secretariate support for both the H-TAG and the HARPS Retailer Committee. One Direction ANZ is not the decision-maker, the HARPS Retailer Committee is the ultimate decision-maker.
It is envisaged that HARPS Version 2.0 will not be released until early 2022, however, this release date is subject to additional review and ongoing refinement by both the H-TAG and the HARPS Retailers, and any other input that may be required, such as pilot audits. The H-TAG have been meeting weekly since February 2021 to review and address feedback, with over 30 meetings completed since the H-TAG commenced.
The Life Cycle of an audit
Food safety audits are a vital part of doing business. Not only do audits help ensure your business is meeting your customers’ standards, but they also help prove that you are adequately following current legislation and this forms an important part of your due diligence defence should anything go wrong. There are many reasons why a food safety audit is good for your business. Audits can:
- Provide direction for achieving business goals for continuous improvement and greater efficiency;
- Analyse the performance of your input suppliers;
- Help meet and stay abreast of regulatory requirements;
- Help to proactively address issues before they occur; and
- Assist in analysing customer feedback and/or complaints to improve your business reputation and performance.
Preparing for your audit can be overwhelming. Whist you are preparing, a great deal of planning and preparation is also taking place from the perspective of your Certification Body (CB), the business that is conducting your audit, as well as the auditor. We’d like to share some insight into what takes place when audits are planned, conducted and recorded, through to issuing the HARPS certificate. Figure 1 below provides an overview of the audit process with additional detail provided below.
Figure 1. An Overview of the Audit Proces
Pre-audit Activity and Scheduling
HARPS audits are typically scheduled up to 3 months in advance of the audit date. Given the availability of auditors and the diverse range of locations required for travel, efficient planning and scheduling is essential to keep travel costs to a minimum. During the scheduling process, CBs will “match” a suitably competent auditor (an auditor that is approved to conduct the audit for the program codes required by the client), consider the site location and ensure there is adequate “auditor rotation” in place; CBs are required to ensure that auditors do not conduct more than three consecutive audits for any one particular business to mitigate any familiarisation with the business and their processes, and COVID restrictions have certainly created more challenges for CBs in this regard!
The auditor will typically contact the site to arrange a suitable date and time, ensuring the appropriate products and activities will be able to be assessed during the audit (it’s important to ensure that the activities included within the audit scope are taking place on the day of the audit, otherwise the audit may not be able to be completed). Once the audit date has been confirmed the audit agenda can be developed and shared with the auditee (the site).
Prior to the audit taking place, the auditor may access the previous audit report to obtain background about the audit outcome and whether there were any specific areas of non-compliance that were raised. If the auditee is a new client, obviously this process will not take place. The auditor will be provided with a copy of the HARPS Audit Summary Page, a document that is downloaded and shared with the auditor by the CB, which details the auditee’s business and trading name, address and contact information, GFSI program to audit, process and product scopes. The auditor will request any additional information they require in preparation of the audit.
The Audit is Conducted
Audits will typically occur over a series of stages, including an opening meeting, a site inspection, review of documentation, review of audit findings and the closing meeting.
The opening meeting is a good time to ensure both you and the auditor agree on the pre-advised agenda for the day. It is also the time to confirm locations that require inspection, personnel that will be required as part of evidence collection for the audit process and any important catch-up times, such as the closing meeting.
It’s critical that the information collected on the HARPS Summary Form is accurate. This includes the retailers that you are supplying (where available), as this information will allow the corresponding retailer to access a copy of the HARPS Summary Form, a summary of the corrective actions and the final HARPS Audit Report. It is worth checking you have clearly stipulated the key contact’s name and email address for your business to ensure they receive the HARPS Audit Report and the HARPS Certificate (and any other communication from HARPS, such as the quarterly HARPS Newsletter). This is also a good time to set an expectation on timing for the closing meeting.
The auditor is there to assess your organisation’s compliance against a set of elements, therefore, it is important that they collect objective evidence to demonstrate how well your business is complying. This means allowing the auditor access to documentation, relevant sites and infrastructure and personnel to build a body of evidence that provides evidence of your compliance.
The closing meeting is when the auditor will share the audit findings. The auditor will share both positive outcomes as well as areas for improvement. The areas for improvement, or non-conformances, should be discussed openly as they are identified during the audit. Final decisions and ratings, such as minor or major non-conformances, should be addressed in the closing meeting along with a discussion on the closeout information required to address the non-conformance(s). The auditor should provide a copy of the corrective actions to the site prior to leaving.
Initial Technical Review and Audit Report
All GFSI-benchmarked audits must be reviewed by an approved Technical Reviewer prior to approval for the CB to release the initial report to the site, this typically takes around one hour for this review to be conducted with additional time for follow up with the auditor and clarification.
The Technical Reviewer is a senior auditor or other suitably qualified person that will review the audit report and corrective actions with a view of independence. They will be looking to ensure the report contains the correct level of objective evidence, that the findings have been described adequately and that the severity ratings have been appropriately classified. In addition to your records (completed forms), the audit report can be used as objective evidence should it ever be required.
The Technical Reviewer is responsible for ensuring that any areas identified as incomplete, or not adequately explained or described, are reviewed with the auditor, so that these findings can be discussed and agreed prior to the report being released to the site.
Final Technical Review, Certification Decision, and Issue of the Certificate
The site then submits all objective evidence and corrective action(s) to the auditor for review and closure of any identified issues during the audit. The auditor and auditee may have further exchanges during this process until the auditor is satisfied any issues identified can be closed. The auditor will submit the final report back to the CB. The final closed report undergoes a final technical review which will take approximately 30 minutes to complete, to ensure that non-conformances have been addressed adequately by the site and closed appropriately by the auditor. The Certification Manager will then review the audit history as part of the certification decision process, which takes approximately 10 to 15 minutes to finalise. This is the final step on approval of the final report.
At this point, the CB Administration will upload the final report, objective evidence and any other information to the HARPS Portal and issue a HARPS Certificate to the auditee. This is sent directly to the auditee via the HARPS Portal, which connects to the HARPS Database that holds all site information.
HARPS Audit Fees and Contributions
HARPS charges a fee of $245.00 + GST for each site that is audited to HARPS, which is collected by the CB on behalf of HARPS, called the HARPS Royalty Fee. This fee has remained unchanged since the launch of HARPS in October 2016. HARPS is self-financing and receives no funding from Hort Innovation, and relies on income from the HARPS Royalty Fee, as well as contributions from the HARPS Participating Retailers, CB’s that audit HARPS and Auditors via an annual registration fee. HARPS is owned by Hort Innovation and managed by One Direction ANZ.
During FY2021 HARPS received funds as follows:
Approximately half of the operating costs of HARPS is from the HARPS Royalty Fee, with the majority of the remaining contribution coming from retailers, CB fees and then the annual registration fees from Auditors.
Other Fees Associated with HARPS
There are a number of fees that your business may incur in certain situations as described below. This information can be found on the HARPS website or by clicking here.
Fee Title | Amount | Fee Description and Collection Process |
---|---|---|
HARPS Royalty Fee | $245.00 | The fee charged to a supplier for each HARPS audit conducted, includes any certification, recertification, surveillance, or unannounced audits that take place for the GFSI program where HARPS is added to the audit. The Certification Body collects this fee on behalf of HARPS. |
HARPS Scope Extension Fee (on-site audit) | $145.00 | The fee charged to a supplier for a HARPS scope extension audit conducted on-site, outside of the regular audit cycle. The Certification Body collects this fee on behalf of HARPS. |
HARPS Scope Extension Fee (desk audit only) | $45.00 | The fee charged to a supplier for a scope extension audit conducted as a desk audit outside of the regular audit cycle. The fee is charged by the Certification Body to their client. The Certification Body collects this fee on behalf of HARPS. |
HARPS COVID Extension Fee | $45.00 | The fee charged to a supplier for a COVID extension. The Certification Body collects this fee on behalf of HARPS. |
HARPS Certificate Re-issue Fee | $45.00 | The fee charged to a supplier for the re-issue of a HARPS certificate due to an amendment, error, or change that is notified to HARPS greater than 5 business days after the initial certificate has been issued. The Certification Body collects this fee on behalf of HARPS or is charged this fee if the error is created by the Certification Body. |
Fees are exclusive of GST |
Get to know the HARPS Technical Advisory Group Members
The HARPS Technical Advisory Group (H-TAG) is a group of industry representatives that are integral to the ongoing development of HARPS. The H-TAG is responsible for guiding and contributing towards improving the operational effectiveness of HARPS, including the HARPS Standard (particularly Version 2.0) and associated technical documents, such as the Interpretive Guidance Document and Scheme Rules. Current membership is comprised of a broad cross-section of industry representatives, including grower-packers (large and small businesses), marketers, Certification Bodies, food safety scheme representatives, as well as industry association representatives and consultants. All members have deep technical experience from within the fresh produce industry.
The H-TAG provides a voice for industry and help develop recommendations to the retailers regarding improvements to HARPS. Through future editions of the HARPS Newsletter, we’ll provide you with the opportunity to get to know who your H-TAG representatives are and why they chose to be a part of this valuable group. In this edition of the HARPS Newsletter, we’d like to introduce you to Deon Mahoney, Head of Food Safety at PMA Australia-New Zealand Ltd, and Wade Mann, Senior Grower at Family Fresh Farms.
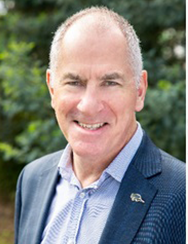
Deon Mahoney
Head of Food Safety, PMA Australia-New Zealand Ltd
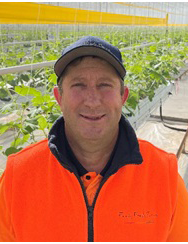
Wade Mann
Senior Grower, Family Fresh Farms
Can you please tell us a little about your role and how your role assists with HARPS?
Deon: The mission of PMA Australia New Zealand is to connect, inform and deliver industry solutions that enhance member’s prosperity. Our members are from every segment of the fresh produce supply chain, from growers through to retailers, across Australia and New Zealand.
As Head of Food Safety, I am involved in supporting members to assure and enhance the safety of their produce. This is achieved through regular food safety webinars, publishing Tech notes, provision of expert advice, delivery of training, and regular food safety community updates. The approach focuses on explaining the why and how of food safety with the goal of unraveling the myriad of food safety challenges and proposing practical solutions.
My role is underpinned by long-term involvement in food microbiology and safety across a wide range of industry sectors, in Australia and overseas. This includes roles in training, quality assurance, establishing and enforcing food standards, and risk assessment.
My involvement in HARPS/H-TAG reflects my passion to enhance food safety. I bring to the Group a broad knowledge of current food safety issues, practical strategies on how to manage food safety, and expertise in food standards and regulations.
Wade: I am the Senior Grower Manager at FFF, focusing essentially on all matters pertaining to the cultivation of 5ha of glasshouse, hydroponic snacking cucumbers. We have the ability to produce snacking cucumbers over 365 days of the year through extensive planning and crop scheduling. As a result, it is imperative we mitigate any potential breaches of food safety to enable our consistency and continuity of supply to our customers.
We are classified as a Tier 2 grower-packer as we value-add through on-farm prepack enabling our finished product to either undertake delivery to our wholesaler or in certain circumstances, direct to supermarket distribution centres (DCs).
In 2015, I was honoured to receive a Nuffield Australia Scholarship, affording me the opportunity to travel globally in pursuit of the latest IPM strategies specifically relating to greenhouse berry crops. The cross-over of this study has been of massive benefit to FFF in reducing our reliance on chemical controls and ultimately providing a safer product for consumption by the end consumer.
How and why did you make the decision to apply as a H-TAG member?
Deon: Becoming a member of the H-TAG provided the opportunity to contribute to the ongoing evolution of the Standard. I felt I was able to provide both an industry view of the practical challenges of implementing and certifying a standard and at the same time balancing that against regulatory and customer requirements for safe food. Guiding the development of the standard and ensuring it remains practical, achievable, and relevant is a significant responsibility and the outcome of this process will benefit both producers and consumers.
Wade: It appeared that representation on the group by Tier 2 growers was subpar and an opportunity for me to contribute to the development of HARPS under this category was imperative. My extensive time in primary production will enable me to offer my experience and views regarding a balanced outcome of the standard required to ensure safe food. The incredible diversity and wealth of knowledge within the group will undoubtedly raise my awareness and understanding of the areas in the whole supply chain that I have not had exposure to, providing me with invaluable insights.
It has been a busy year for HARPS given our review of the Draft Version 2.0 HARPS Standard. Could you describe your experiences on the H-TAG so far?
Deon: The H-TAG process continues at pace and real progress is being made. The process has been rigorous, with frank and candid discussions on key issues. The representation within the group adequately matches the diversity across the horticulture sector, and the challenge to accommodate diverse views and competing interests of the members has been handled well. There is a very collegiate spirit among the majority of members.
Significant issues have been very effectively handled by establishing small working groups to tease out an issue, identify ways to move forward, then bringing the findings back to the H-TAG for decision.
I probably did not fully appreciate the magnitude of the task at the outset. But we are working systematically through the HARPS Standard and addressing all the feedback on the proposed changes. During this process, we are building a body of evidence that will support key changes.
Wade: Whilst I was not a founding member of H-TAG, I have been warmly embraced as a Tier 2 representative and astounded at the cross-section and diversity of my fellow members creating this dynamic team. The ability of this group to dissect and tease out the finer points of the Draft Version 2.0 to ensure the brief is being covered adequately, in an open and collaborative manner has been commendable.
This task has been far more demanding than I originally envisaged, suffice to say that the group have assumed the necessary responsibility to ensure every minute detail has been covered, and ensuring progress in the right direction.
Perhaps the greatest challenge we must overcome is providing a Version 2.0 that is simple to follow, easily understood and practical to implement. It is incumbent upon us to create a HARPS Standard that is not dismissed as too onerous or confusing and thereby compromising food safety through substandard practices.
Finally, what do you think are some of the broader challenges we face as an industry as far as food safety is concerned?
Deon: Assuring food safety remains a major challenge for the fresh produce sector. FSANZ has put the industry on notice, with Proposal P1052 – Primary Production and Processing (PPP) Requirements for Horticulture (Berries, Leafy Vegetables and Melons) considering the need for regulatory and non-regulatory food safety risk management measures.
The entire horticulture industry needs to re-examine how it manages the safety if its products – including how it controls its inputs, the training and skills of personnel, and the systems and programs that oversee food safety. Consumers demand fresh produce that is safe, and this needs to be nurtured, because every incident has an impact on consumer confidence and market access.
Unfortunately, the incidence of illness attributed to fresh produce is on the increase. So, in addition to better managing food safety, we need to also focus on the culture of our food businesses. An organisational culture that values, respects, and nurtures their staff is better able to assure the safety of its products.
Wade: Food safety is of paramount importance to the end consumer. In this light, it is essential that the necessary time and resources are devoted to establishing a food safety culture through ongoing training and personal development, commencing at the primary producer level and flowing throughout the supply chain until the end consumer. It is of vital importance that there is “buy-in” at every step of the supply chain to maintain the integrity of safe food.
The adoption of the HARPS standard may very well appear overwhelming at the outset. However, it should be viewed as an investment in food safety. As the process is undertaken, it is evident that there are sections in the standard that may be used as key performance indicators and ultimately increasing efficiencies and effectiveness in providing safe food. Food safety is not negotiable, and we need to embrace the demands of the standard to comply and fulfill our obligation in providing a safe product. In my mind, “he who hesitates, disintegrates”.
Interested to hear more? Deon has written a great article on a proactive approach to food safety, thinking about food safety as an investment rather than a cost to your business. Click here to read Deon’s article.
HARPS Logo available to Industry Members
Would you like to use the HARPS logo on your website, non-customer facing packaging or other B2B communication? The logo is available to businesses that are audited to HARPS along with industry organisations interested in using the logo for marketing purposes. For further information on the rules for use and the annual fee, please click here. To apply to use the logo, click here.