HARPS Newsletter April 2022 Edition
In addition, we’ll introduce you to another H-TAG member, Annmarie Schwanke of Merieux NutriSciences, to find out why she joined the H-TAG and what she hopes to bring to the group.
We would like to take this opportunity to inform you of an increase to the HARPS Royalty Fee. From 1st July 2022, the Royalty fee for HARPS audits will increase from $245 to $295, plus GST. This fee has remained unchanged since the launch of HARPS in October 2016 and takes into account CPI inflation, as well as the development of tools and training to support the release of the Version 2.0 standard.
ACO Certification Ltd is a recent addition to the list of HARPS-approved Certification Bodies. You can review the available HARPS-approved Certification Bodies and their key contacts here. We caught up with Mark Shaw, Executive General Manager at ACO Certification to gain insight into their desire to join the list of HARPS approved Certification Bodies, and what value they bring to industry.
Feel free to share your thoughts, opinion or queries with HARPS by clicking here or contacting the HARPS Helpline on 1300 852 219.
Update on HARPS Version 2.0
We are now in the final review stages of the HARPS Version 2.0 Standard. The HARPS Technical Advisory Group (H-TAG) has methodically worked through the feedback received during the HARPS Version 2.0 public consultation in January 2021.
In addition to the removal of the section on Business Culture, the retailers have agreed to remove the section on Food Fraud and Food Defence given that these areas have been adequately addressed by the GFSI benchmarked standards.
We will now pilot the draft standard to ensure it is practical and suitable for the activities conducted by the businesses being audited to HARPS. The final draft will then be available for review by industry, where feedback can be provided regarding technical aspects within the HARPS Standard & Guidance Document and the Scheme Rules. We anticipate the release of Version 2.0 to be later this year, with a 6 month period for sites to transition from Version 1.0.
We will continue to update the HARPS Website FAQ page to provide responses to your questions and feedback, including the concerns raised during the public consultation process. An ‘update date’ has been added to the FAQ page with new FAQs prefaced with ‘[NEW]’ to assist readers to identify and review new FAQs more easily. In addition, we will continue to provide updates via the HARPS Newsletters. If you have not yet subscribed to the Newsletter, we encourage you to do so by clicking on the following link, subscribe to HARPS.
Review Process facilitated by HARPS Management
Increase to HARPS Royalty Fee from 1st July 2022
There will be an increase in the price of the HARPS Royalty Fee from $245 + GST per audit to $295 + GST, to take effect on 1st July 2022. The HARPS Royalty Fee has remained unchanged since the launch of HARPS in October 2016 and will continue to be collected on behalf of HARPS by your nominated HARPS-approved Certification Body.
Our aim is to ensure costs for all suppliers remain fair and reasonable and that any increase does not create a barrier for suppliers to achieve HARPS approval. The fee increase has been closely considered, taking into account CPI inflation and the development and launch of Version 2.0 of the HARPS Standard, together with industry support via guidance documents and training.
The Royalty Fee, together with contributions from the HARPS Participating Retailers, Certification Bodies and Auditors, helps to ensure an ongoing commitment to delivering a harmonised standard that aligns the food safety, trade, and legal requirements of the major retailers in Australia for the supply of whole fresh produce and nuts in-shell.
If you have any questions about the above changes, please contact harps@harpsonline.com.au or call the HARPS Helpline on 1300 852 219.
Introducing ACO Certification
ACO Certification Ltd has recently joined the list of approved Certification Bodies for HARPS. An increase in Certification Bodies is positive for industry since it creates greater availability of auditors and increases competition between our approved auditing bodies that can result in a more competitive pricing for businesses being audited to HARPS.
Mark Shaw is the Executive General Manager at ACO Certification Ltd and we took some time out with Mark to discuss some topical questions.
Mark, can you provide us with some background on ACO Certification Ltd and the role your business plays in the Horticulture Industry?
ACO Certification, formerly known as Australian Certified Organic, are Australia’s largest certifier for organic products. ACO certifies over 2,000 primary producers, livestock operators and processors. ACO added Freshcare certification to our services 6 years ago in response to interest from our organic operators. We have since broadened our services to include Freshcare FSQ, Freshcare Australian Wine Industry Sustainability certification and HARPS to existing organic growers and new conventional growers. ACO aims to grow our scope of services, including Supply Chain, and national network of auditors to provide food safety and sustainable certification solutions for our operators.
From a certification and auditing perspective, can you explain how Organics is different to conventional produce?
From a food safety perspective, there is no difference in the audit and certification process for organic or conventional producers.
Organic certification allows market access where verification of compliance with various Organic Standards is required.
Why did ACO Certification Limited want to conduct HARPS audits?
Food Safety auditing has been a steadily growing part of our business for several years and was originally introduced to provide efficiencies for our organic operators.
Most operators continue to experience increasing demands on their time and are looking for more efficient ways of completing their audit. As a consequence, we have seen a steady increase in requests for combined Organic, Freshcare & HARPS audits from our organic operators.
We have also been offering Freshcare certification to conventional producers since 2019 and have had an increasing number of requests for combined Freshcare and HARPS audits from these operators.
Can you tell us a little about your team, i.e., who suppliers can expect to speak with if they would like to understand more about ACO Certification Ltd and your capabilities? How can they reach your business?
ACO has a dedicated food safety team who can assist operators through their certification journey from the point of application. The best contact to reach out to with any questions is Ruwi Jayasuriya on (07) 7350 5706 or via email at ruwi.jayasuriya@aco.net.au
Industry may argue that all Certification Bodies are the same, perform the same tasks etc, what are some of the tangible or intangible attributes of ACO Certification Ltd that set your business apart from others?
ACO can provide certification services to suit our operators’ diverse requirements including Organics, Sustainability and Food Safety certifications. We are a service and solutions focused organisation that understands the needs of our operators and works with them throughout the audit and certification process.
ACO also currently conducts the CAR closure process in-house which results in reduced costs and more consistent outcomes for operators over time.
From time-to-time we hear from businesses that tell us their auditing experience is very inconsistent between one auditor and the next. How does ACO Certification Ltd mitigate this concern?
ACO has a robust auditor training program, which consists of routine calibration sessions. ACO provides continuous feedback and areas for improvement to our auditors and supports them with their training and professional development needs.
What are your thoughts on digitisation in auditing, i.e., moving from face-to-face to a more remote stye of auditing for food safety? Is there any work being conducted by ACO Certification Ltd in this space?
ACO has become very proficient in delivering remote audits due to the challenges created by the pandemic and natural disasters such as bush fires and floods. ACO has provided training to our auditors on remote auditing and the use of technology to make remote audits as effective and detailed as possible. We also understand the nuances around sharing information, confidentiality and data protection and require our auditors to handle operator information with confidentiality.
Spotlight on H-TAG Members
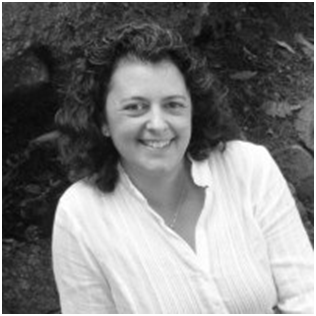
Annmarie Schwanke, Technical and Certification
Manager at Merieux NutriSciences
The HARPS Technical Advisory Group (H-TAG) is a group of industry representatives that are integral to the ongoing development of HARPS. The H-TAG is responsible for guiding and contributing towards improving the operational effectiveness of HARPS, including the HARPS Standard (particularly Version 2.0) and associated technical documents, such as the Interpretive Guidance Document and Scheme Rules.
The H-TAG provides a voice for industry and help develop recommendations to the retailers regarding improvements to HARPS. Membership of the H-TAG is from across various industry sectors and activities. Our members have varied responsibilities across the supply and all work together to deliver safe fresh produce to retail customers. In this edition of the HARPS Newsletter, we’d like to introduce you to Annmarie Schwanke, Technical and Certification Manager at Merieux NutriSciences.
Annmarie, tell us a little about your role with Merieux NutriSciences and how your business provides services for HARPS?
Merieux NutriSciences is a full-solutions service provider to the horticulture industry offering third party certification against all of the Base Schemes that are approved for HARPS in conjunction with the HARPS Addendum. We also have four NATA accredited laboratories across Australia providing analytical testing services that certify compliance with regulatory and industry requirements. We offer digital solutions, environmental monitoring and packaging testing. As the Technical and Certification Manager, my role is to ensure that our auditors are qualified professionals and consistent in the application of the standard requirements to each site they visit. I am also responsible for ensuring Merieux NutriSciences meets compliance requirements and delivers effective and efficient services to industry.
I have been working in the Food Safety and Certification industry for over 20 years now in various roles both nationally and internationally. Program Management has been the primary role, but I have also worked in training (RTO) and Quality Management across both food and non-food industries. HARPS is an integral part of the horticulture side of the business with almost 45% of the sites we audit requiring a HARPS audit component. With Retailers accepting the HARPS report in lieu of their own Customer audits, for the most part HARPS has reduced the number of reports each auditor has to complete for the site.
How and why did you make the decision to apply as a H-TAG member?
I wanted to be a member of the H-TAG to represent the Certification Bodies and Auditors as often our experiences in the application of the standard in a practical way can be overlooked. Utilising my own personal work experiences and knowledge it was a great way to provide back to the industry. As a Certification Body, we work with small- and large-scale facilities, take on the feedback from auditors and sites that sometimes otherwise would not be heard, and I felt it was important to share that perspective. For me personally it is exciting to have an opportunity to have input into shaping the next phase of the standard. As other H-TAG member have stated, I am passionate about the Food Safety Industry, and it is rewarding to be able to contribute in a positive way.
Can you tell us about your experiences on the H-TAG so far?
The H-TAG is a very dynamic, diverse, and dedicated group of individuals (Tier 1, Tier 2, Auditors, CBs, Trainers, Standard Owners, and Grower Groups etc.) who all have a passion for this industry and want to see horticulture flourish in years to come. We have had some very lively debates and difference of opinion or approach to certain elements in the new standard, but I think the group has done a great job of respecting each other and understanding that in the end we all want to add value to the process and make improvements to the standard. The members are very dedicated, volunteering countless hours over the months as the review of Version 2.0 took shape.
For me it has been a very positive experience because I would like to think that not only have I had an opportunity to speak but I have had the opportunity to listen to other points of view. As a group, we have really tried to find common ground and make recommendations back to the Retailers that will benefit all producers. I think the biggest challenge at hand is changing opinions and perceptions within industry that have grown over the last 5 years about HARPS. I think it is very important for industry to understand that the H-TAG’s role is to make recommendations back to the Retailers for acceptance and adoption, but it is the Retailers that have the final decision on what the standard will look like based on their requirements.
Finally, what do you think are some of the broader challenges we face as an industry as far as food safety is concerned?
One of the biggest challenges we face is adoption. What do I mean by that? In the last 5 to 7 years, standards have changed quite a bit and have introduced more rigour and defined concepts more soundly (like food safety culture, food fraud, food defence, Management Commitment). There is a feeling that the standards are adding more but compliance is in fact sliding because it has become too burdensome for some producers. Many producers struggle because they are a small operator and do not have a dedicated Quality Manger or Quality Team as well as the fact that many have seasonal staff and staff turnover which can impact staff training, consistency and food safety culture.
FPSC launches new food safety resources
The Fresh Produce Safety Centre (FPSC) and Freshcare have launched three new food safety flyers for the Fresh Produce Industry. The flyers are easy to follow and are tools to help businesses across the supply chain understand specific chapters from the Guidelines for Fresh Produce Food Safety.
Chair of the FPSC, Dr. Andreas Klieber, said: “We are keen to promote tools and resources to help everyone in our industry understand the key food safety issues and the practices we need to follow to produce safe, quality food, day in and day out.”
The three flyers focus on:
• Managing water
• Managing chemicals
• Managing people
The FPSC plans to produce more flyers on other topics from the Guidelines for Fresh Produce Food Safety.
The flyers are here.